CNCI have been continuing the work on mill retrofit.
The Control Box has been completed. I gave it a coat of paint, installed all the components and wired them up.
I purchased a used computer a few months ago that I am using to control the mill. So I intalled Mach3 on it, and tested out my wiring.
Some simple tests have shown that the Control Box works. The G540 through Mach3 is able to activate the relays for the spindle and flood coolant controls.
As far as the mill itself goes. There are a few of things I have done:
1. Base. Currently the mill was on a 3/8" of steel plate that was bolted to the original box. I fabricate a base out of 2"x2" steel tube and 1/8" steel plate. The idea being that the mill sits on this and this base is bolted to the mill stand.
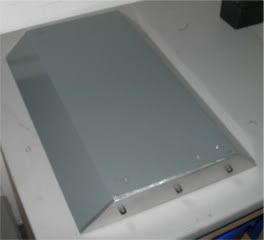
2. Anti-backlash. Using compression springs and thread Delrin blocks, I was able to devise an anti-backlash mechanism that I hope will improve the accuracy of the mill. The compression of the springs between the delrin block and the bronze nut yields almost 50lbs.
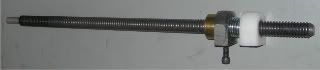
3. Motor mounts. On the x and y axis, I improved upon the motor mounts. I used aluminum standoff blocks, whereas the previous ones used a metal box that wasn't as secure.
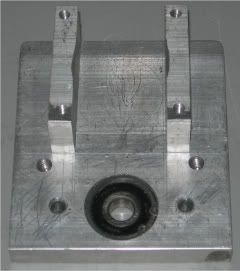
4. Cover. Because coolant eventually will be used on the mill, the exposed x axis motor needs to be protected. So a cover was fabricated from sheetmetal.
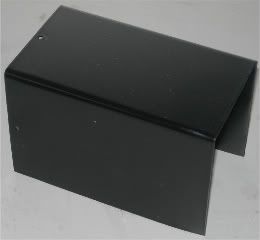
5. Paint. The mill has been painted, improving upon the colour scheme originally used.
6. Stepper Motors. The motors have been wired up, and just need to be plugged into the Control Box for testing.
Things left to do:
1. Assembly. Put the mill together.
2. Tooling Plate. I picked up a piece of 15" x 6" ALCOA MIC6 plate that will be used as a tooling plate. A matrix of drilled and tapped holes addd to it, and then it will be bolted to the mill table.
3. Limit Switches. After the mill is assembled and operational, limit switches will be installed.
4. Mill Stand. Need to construct a workbench that the mill will sit on, and eventually build an enclosure for it.