Through an aquaintance of mine, I was able to get as a freebie (I actually traded for it with a few cans of espresso beans) a used semi-functioning mill.
The history of this machine is that it was used up until seven years ago in an Ontario high school tech program. So this mill is a light-duty training model.
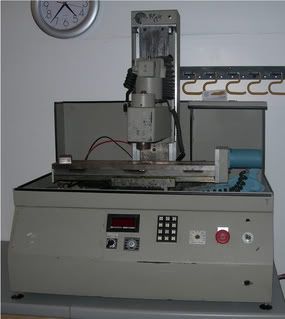
I have been interested in CNC Milling technology for quite a while, I just never had the time/opportunity to explore it as much as I would have liked. But now that I have my own mill, I am quite eager to get into it.
I have a number of parts that I would like to create for my motorcycles. So the goal is to get it fully functioning for Summer 2009.
The specifications on the mill as it is now:
- Travel (x, y & z): 12" x 6" x 3"
- Spindle Type: R8
- Spindle Motor: <1/5hp
- Spindle RPM Range: 0 - 2500
- Controller: Proprietary driver board and controller (6800 microprocessor based it seems).
- Cutting speed: <5 IPM (Inches per Minute)
The base of the mill contains all the driver circuitry and the controller boards. Quite ancient stuff in comparison to what is available today.
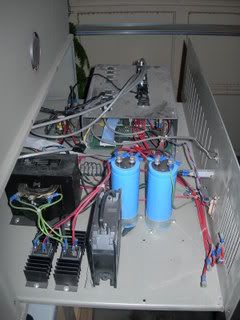
I started the teardown of the mill, and junked alot of what was in the base. I kept all the power supply parts (transformer, rectifiers, capacitors etc) because those are usable.
The controls (E-Stop, power switch, tach display) on the front of the base were kept as well. Those along with the power supply parts will be used in the refurbishment process.
The ways (X and Y) were dissassembled and cleaned. I have started to lap the ways to make them smoother operating. Lapping is a very fine grinding process used to even out surface irregularities on parts that seat together. The smoother the ways are the better the mill will function in terms of efficiency and accuracy.
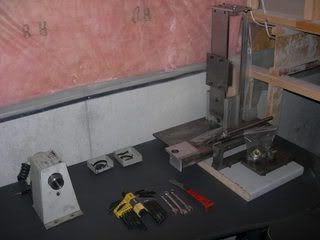
The end goal of the refurbishment process is to have a mill that is more powerful, efficient and accurate. Here is a list of the things that will be done to the mill:
- Stepper Motors. NEMA 23 250-300oz-in motors will be installed that will be an improvement over the 100oz-in that it came with.
- Controller and Driver. A Gecko G540 Controller/Driver unit will interface to the stepper motors and to the PC to drive the mill.
- Control Software. Mach3 software will be installed on the PC and will control the mill through the parallel port on PC to the G540.
- Limit & Home Switches. These switches will provide for a way to home the mill when starting on a workpiece, and a safe way to stop an errant mill.
- Stand and Splashguard. A mobile stand that allows the mill to be moved as need be, and a splashguard and/or full enclosure to contain chips and coolant during machining.
- Flood Control. Automatic control of coolant during the machining process.
- Anti-backlash. Put some anti-backlash nuts on the ACME leadscrews on the X and Y axises to reduce the backlash to < .002".
No comments:
Post a Comment